The process is leading
Roof inspection“As easy as pie. If not, we haven't done our job properly.”
|
Decisions about maintenance activities that are to be planned are often based on priorities. Problems with roof inspections often relate to the variation in the results. The causes include the fact that different inspectors make different assessments of defects and their consequences. For example, how is your own roof inspected and that of someone else? Moreover, the instructions are not always clear or the knowledge and skills of the inspector are insufficient. A solution is condition measurement in accordance a standard, which ensures commonality and makes it possible to visualize both the desired quality and the actual quality. The condition measurement is a uniform inspection method with predetermined maintenance levels. A Multi-Year Maintenance Plan (MYMP) can be linked to this, in which the costs of maintenance are related to return aspects. |
State of the art Incorporation of state-of-the-art technology. Fast in operation Basic version within a few weeks. Grows along Scales along with your future ambitions. |
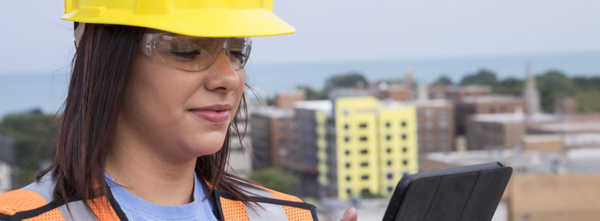
AssumptionsBefore Wikibase Solutions started developing a roof application for condition measurement, a number of assumptions were made about the roofing industry that were later not entirely correct. Eric/Jan van Kakerken:
|
Added valueThe added value of this webapp is its speed and the fact that it ensures a uniform way of working. Van Kakerken:
Working with the software of the roof application does not cause any problems. Van Kakerken: “The system navigates itself. Although it is possible, we have never had to organize training for it. As easy as pie. If not, we haven't done our job properly. Data stored by another system can, to the extent that it can be exported, be imported into the new tool. No problem. This allows you to record the history of the inspections and therefore the documentation. From quick scan to complete reference work. Updates are free and download automatically. As soon as we develop something, it can be followed by the client. He can see every day what phase the development is in. If necessary, adjustments can be made in the meantime. At the end of the ride everything functions flawlessly. The roof application speeds up and simplifies the work flow. Roofing companies can serve their customers more quickly and, regardless of the inspector, are always able to comply with the condition measurement in accordance with the chosen standard.” |
![]() |
The Wikibase stackThe Wikibase stack builds on MediaWiki. With Open CSP MediaWiki is turned into an enterprise level Content Services Platform. Wikibase CSP is Open CSP with additional features that fit in our ecosystem. Our current products:
The customer solution that fits like a glove. |
|